Qualitätsprobleme nachhaltig reduzieren
Veröffentlicht am 20.03.2025 von Bostjan Dolanc
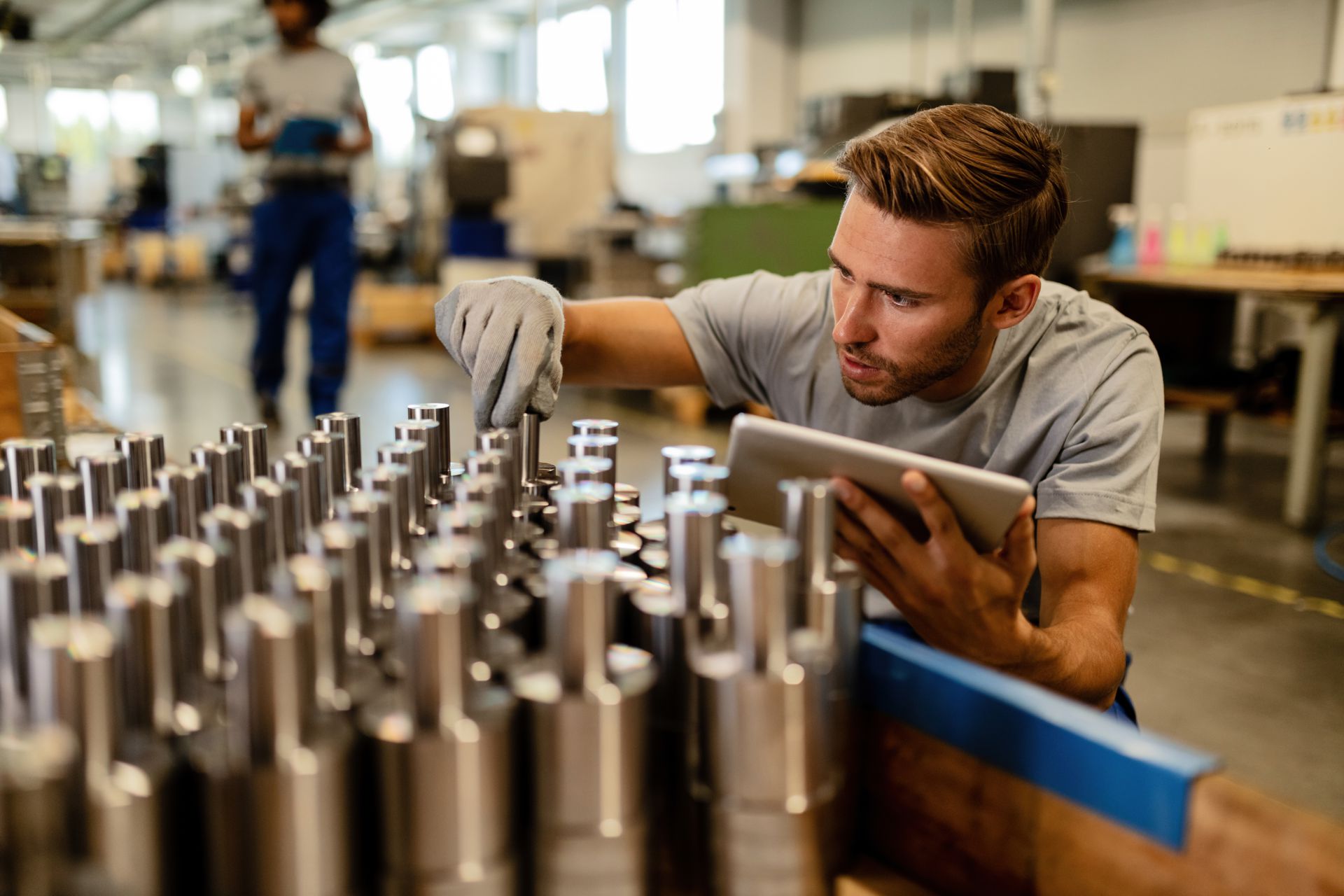
Qualitätsprobleme erkennen
Wer Ausschuss und Nacharbeit reduzieren möchte, braucht funktionierende Qualitätsregelkreise sowie einen einheitlichen Qualitätsmaßstab innerhalb der Belegschaft. Grundvoraussetzung hierfür sind verlässliche Daten in einer hohen Qualität. Wie Sie diese erzeugen und welche Möglichkeiten es hierfür gibt, erfahren Sie in diesem Artikel.
Ausschuss und Nacharbeit ist in vielerlei Hinsicht ein Problem für Unternehmen. Wird eine Abweichung der Kundenerwartungen intern erkannt, führt dies zu Mehrkosten durch Reparatur oder Neuanfertigung. Solche Reparaturen und Neuanfertigungen haben zudem eine negative Auswirkung auf die Liefertermintreue von Aufträgen anderer Kunden. Wird ein Qualitätsproblem hingegen vom Kunden selbst entdeckt, führt dies neben finanziellen Auswirkungen zu sinkender Kundenzufriedenheit und Imageverlust.
Es geht also zunächst primär darum, die Qualitätserwartungen des Kunden zu verstehen und Abweichungen davon zuverlässig im Herstellprozess zu erkennen.
Qualitätserwartungen in Sollvorgaben übersetzen
Eine reproduzierbare und objektive Beurteilung der Qualität kann eine Mitarbeiterin oder Mitarbeiter nur leisten, wenn klare Sollvorgaben aus den Qualitätserwartungen des Kunden abgeleitet sind und zur Verfügung stehen.
„Die Differenz zwischen Ist und Soll ist ein Problem“ Niklas Luhmann, Soziologe
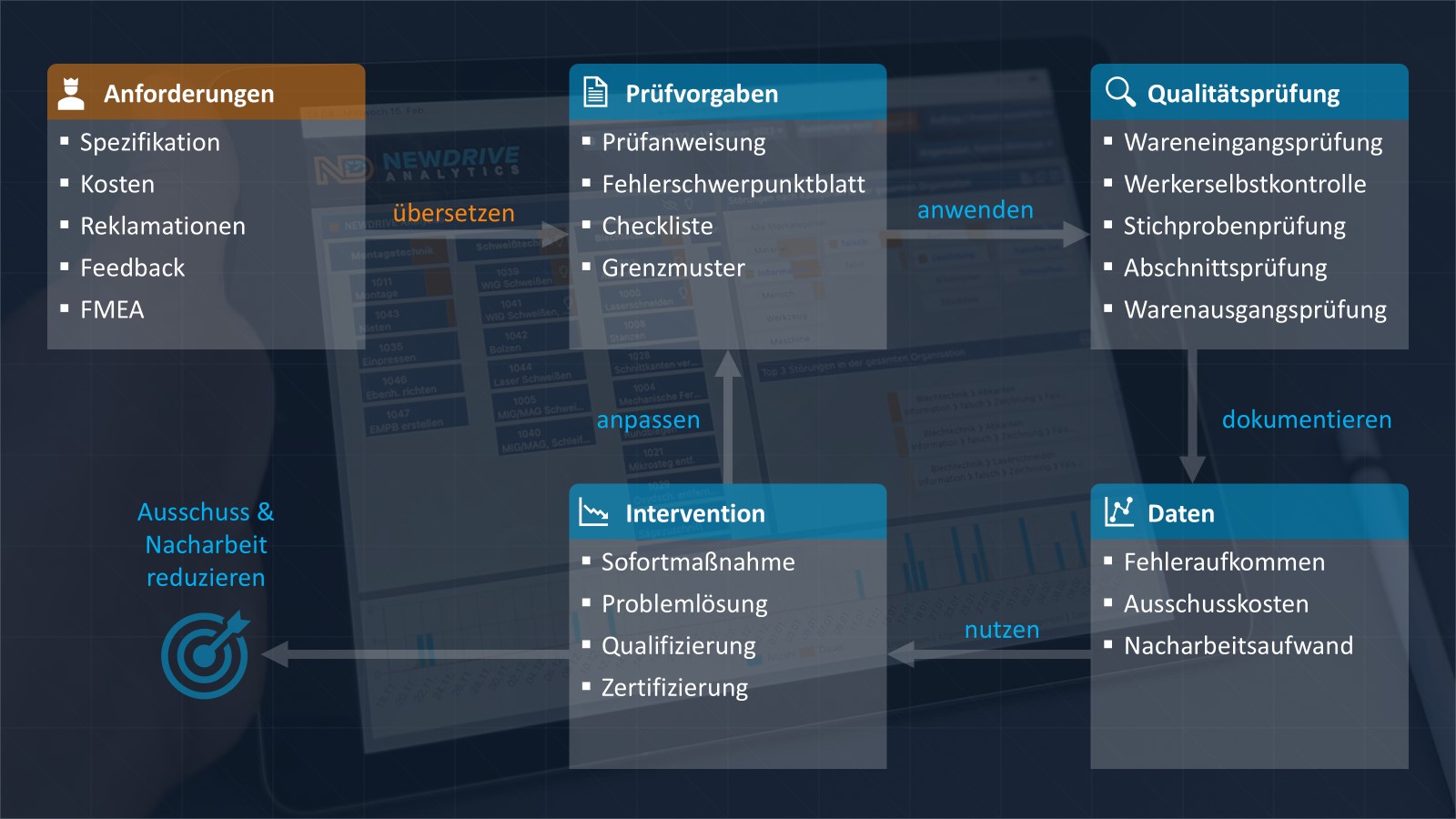
Sollvorgaben aus Erwartungen entwickeln
Klarheit über das Soll kann erzeugt werden durch:
- Eine gemeinsame Festlegung von messbaren Spezifikationen mit dem Kunden (z.B. Maß- & Form- oder Lageabweichung, Oberflächenrauigkeit etc.)
- Historische Daten von Kundenreklamationen
- Einen etablierten Feedbackprozess
- Ergebnisse aus Fehler-Möglichkeiten-Einfluss-Analysen (FMEA)
Damit die definierten Sollvorgaben zu einem einheitlichen Qualitätsmaßstab in der gesamten Belegschaft führen, müssen diese Sollvorgaben in geeignete Dokumente und Hilfsmittel übersetzt werden. Diese gilt es dann in einem zweiten Schritt für den Arbeitsalltag verfügbar zu machen, damit Abweichungen vor Ort im Rahmen der Qualitätsprüfung in der Produktion erkannt werden können. Einige Beispiele für geeignete Dokumente und Hilfsmittel sind in der nachfolgenden Tabelle aufgelistet:
Prüfung | Dokument | Zweck |
---|---|---|
Werkerselbstkontrolle | Arbeitsanweisungen mit Checklisten | Verfahrensanweisungen mit integrierten Checklisten sorgen für einheitliche Prüfabläufe |
Abschnittskontrolle | Referenzmuster und Grenzmuster | Physische oder digitale Beispiele helfen bei der Beurteilung |
Warenausgangskontrolle | Fehlerkatalog mit Prüfprotokoll | Sammlung möglicher Fehler, welche an einem Produkt oder in einem Prozess auftreten können. |
Qualitätsprobleme erkennen
Zur Erkennung von Qualitätsproblemen werden Qualitätsregelkreise installiert, mit der sowohl die Produktqualität wie auch die Ausführung der Tätigkeit (Prozessqualität) überwacht wird. Diese sind Grundlage für ein prozessorientiertes Qualitätsmanagementsystem (QMS) mit einem kontinuierlichen Verbesserungsprozess (KVP) welches durch DIN ISO 9001:2015 gefordert wird.
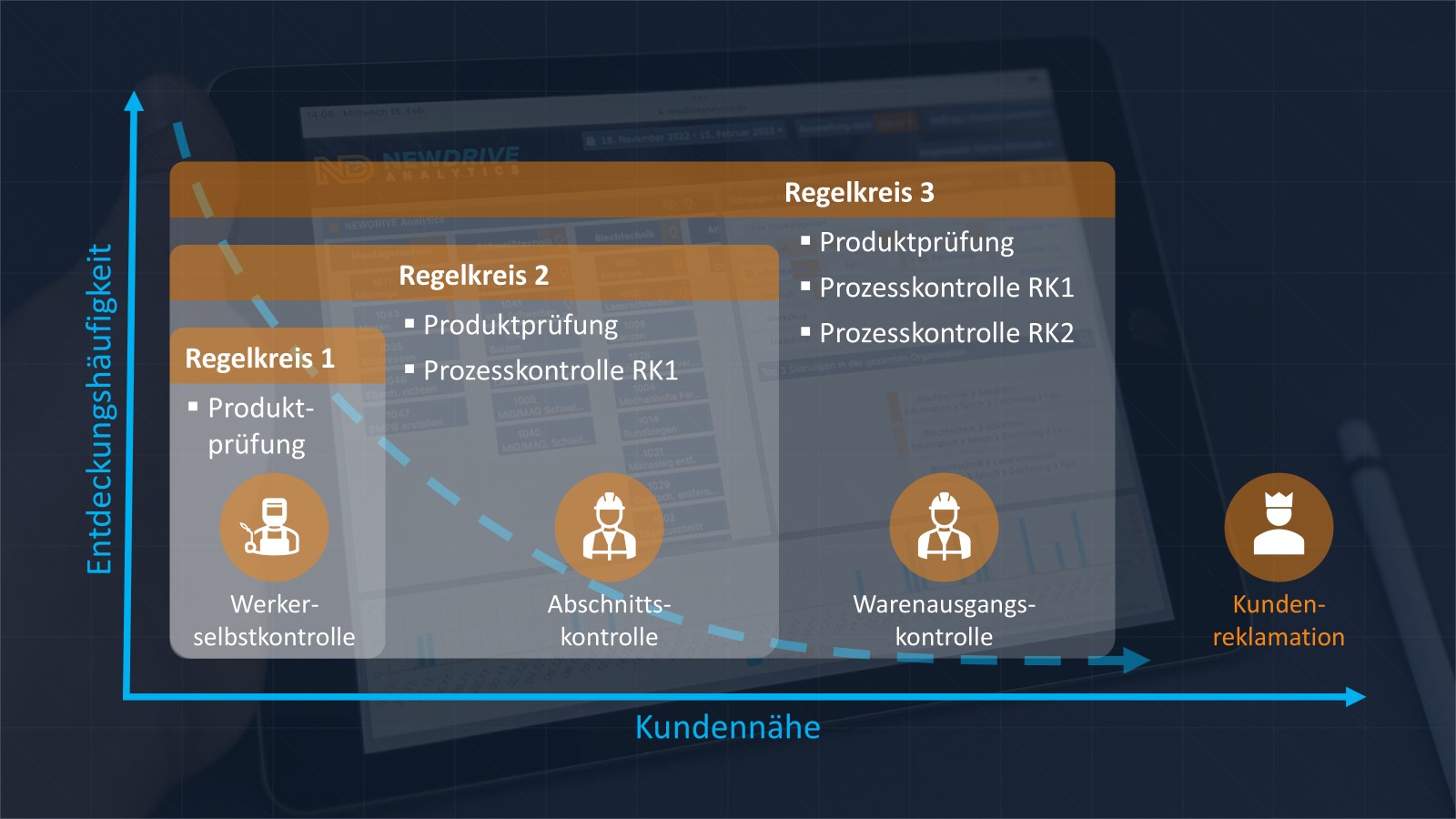
Qualitätsregelkreise
Qualitätsregelkreise basieren auf dem Prinzip des Plan-Do-Check-Act (PDCA)-Zyklus und sorgen dafür, dass Qualitätsabweichungen frühzeitig erkannt und korrigiert werden. Typischerweise bestehen Qualitätsregelkreise aus Sensoren für die Produktprüfung, wie z.B. Werkerselbstkontrolle, Abschnittskontrolle und Warenausgangskontrolle sowie aus Prozesskontrollen, mit der die Ausführung der Tätigkeit inklusive der Produktprüfung (Sensor) überwacht wird (siehe Grafik).
Neben der frühzeitigen Fehlererkennung und der dadurch vermiedenen Folgekosten, dienen Qualitätsregelkreisen auch dazu, den Prüfaufwand auf Grundlage von Qualitätsdaten wie z.B. dem Fehlerschlupf (vom Sensor nicht erkannte Fehler) regelmäßig zu hinterfragen und eine ausgewogene Balance von Aufwand und Nutzen bei den Qualitätsprüfungen sicherzustellen.
Ausschuss und Nacharbeit dokumentieren
Aus unserer Erfahrung wird der Mehrwert einer hochqualitativen Dokumentation von Qualitätsproblem in großen Teilen der Industrie unterschätzt und häufig nur zur Erfüllung von Audits implementiert. Natürlich können Dokumentationsprozesse als ein notwendiges Übel verstanden werden. Daher ist es wichtig eine qualitativ hochwertige Datengrundlage zu erzeugen und dabei den Aufwand für den Dokumentationsvorgang so gering wie möglich zu halten. Doch wenn man die Chancen betrachtet, welche sich aus einer guten Datenbasis ergeben, wird klar warum es sich lohnt an dieser Stelle Zeit zu investieren.
- Grundlage für die erfolgreiche Ursachenanalyse und nachhaltige Problemlösung
- Basis für die Anpassung oder Intensivierung von Qualitätsprüfungen
- Input für die Weiterentwicklung von Dokumenten und Hilfsmittel zur Qualitätsprüfung
- Grundlage für die Ermittlung von Ausschuss- und Nacharbeitskosten
- Input zur Sensibilisierung von Mitarbeiterinnen und Mitarbeitern
- Grundvoraussetzung für eine Rückverfolgbarkeit und erfolgreiche Zertifizierungen
Der Weg, wie man zu einer qualitativen Dokumentation z.B. von Ausschuss und Nacharbeit kommt, kann sehr unterschiedlich sein. Einige Unternehmen nutzen hierzu Fehlersammelkarten, Ausschuss- und Nacharbeitsprotokolle oder Nacharbeits- bzw. Reparaturaufträge. Die Dokumentation reicht von einfachen Handaufschrieben bis hin zu volldigitalisierten Lösungen.
Handaufschriebe bringen aus unserer Erfahrung jedoch einige Nachteile mit sich. Die Datenqualität ist im Vergleich zu digitalen Lösungen schlechter, da die Lesbarkeit, Vollständigkeit und einheitliche Nomenklatur stark variieren. Um die Handaufschriebe weiterverarbeiten zu können müssen diese aufwändig digitalisiert werden. Zudem zeigt sich in der Praxis, dass Handaufschriebe bereits bei der Erfassung einen höheren zeitlichen Aufwand mit sich bringen.
Unabhängig ob analog oder digital – das Wichtigste bei der Erfassung von Qualitätsproblemen ist die Bereitschaft aller Beteiligten, diese konsequent und vollständig zu erfassen. Lesen Sie dazu auch unseren Artikel: „Effizienz und Qualität in der Produktion datenbasiert verbessern“.
Die 10 wichtigsten Informationen bei der Erfassung eines Qualitätsproblems:
- Erfasser
- Zeitpunkt der Entdeckung
- Ort der Entdeckung
- Fehlerbeschreibung
- Betroffenes Produkt
- Betroffener Auftrag
- Anzahl betroffener Teile
- Anzahl Reparatur und Neuanfertigung
- Aufwand für Reparatur oder Neuanfertigung
- Verursacher
Die Merkmale 1-7 werden direkt bei der Erfassung dokumentiert. Die übrigen drei Merkmale werden in der Regel im Nachgang von der Qualitätssicherung analysiert und dokumentiert. Darüber hinaus ist es wichtig, dass das betroffene physische Bauteil so gekennzeichnet wird, dass es nicht versehentlich in den nächsten Prozessschritt oder zum Kunden gelangt.
Für die weitere Bearbeitung des Qualitätsproblems wie z.B. der Nacharbeit, hat es sich bewährt, alle relevanten Informationen direkt am Bauteil verfügbar zu machen. Hierzu können entweder die erfassten Daten in Papierform beigelegt werden oder ein Barcode stellt die Verknüpfung zu einem digitalen Datensatz her, welche z.B. mit einem Smartphone abgerufen werden kann.
Ausschuss und Nacharbeit reduzieren
Neben der einfachen und strukturierten Problemlösung, welche wir in einem separaten Artikel ausführlich behandeln werden, wollen wir in diesem Artikel den Faktor Mensch näher betrachten.
Wir erleben häufig, dass Kundenreklamationen oder erkannte Qualitätsprobleme durch das interne Qualitätsmanagement nicht oder nicht in einer geeigneten Form an die Mitarbeiterinnen und Mitarbeiter zurückgemeldet werden. Dadurch wird der Belegschaft die Chance genommen, den persönlichen Qualitätsmaßstab mit den Kundenerwartungen abzugleichen und anzupassen.
Problematisch wird es insbesondere dann, wenn sich Qualitätssicherung und Führungskräfte allein um Qualitätsprobleme und Kundenreklamationen kümmern, ohne den Verursacher darüber zu informieren oder einzubinden. Ohne diese Information kann der betroffene Mitarbeitende jedoch kaum ein Verantwortungsbewusstsein für die Qualität seiner Arbeit aufbauen.
In diesem Kontext gibt es zwei Ebenen, wie Qualitätsprobleme kommuniziert werden sollten. Zum einen muss unmittelbar nach bekannt werden eines Problems, der verursachende Mitarbeitende informiert werden, um weitere Fehler zu vermeiden. Dabei geht es darum, dem Betroffenen die Chance zu geben, aus dem entstandenen Fehler zu lernen und seinen persönlichen Qualitätsmaßstab anzupassen.
In der zweiten Ebene geht es darum, aus den Erkenntnissen zurückliegender Qualitätsprobleme die gesamte Belegschaft zu sensibilisieren. Dabei empfehlen wir Kundenreklamationen und intern erkannte Qualitätsprobleme im Rahmen standardisierter Rückmeldeprozesse an die Belegschaft zurückzumelden. Als geeigneter Rahmen für solche Qualitätsrückmeldungen hat sich eine Tages- oder Schichteinstimmung oder eine wöchentlicher Qualitätsregeltermin bewährt. Dabei geht es vor allem darum eine Kultur zu etablieren, in der jedes Qualitätsproblem als Chance begriffen wird, um besser zu werden und jedes erneut aufgetretene Qualitätsproblem zum Anlass genommen wird, die eigene Problemlösefähigkeit zu reflektieren und weiterzuentwickeln.
Fazit
Die Reduktion von Ausschuss und Nacharbeit erfordert klare Sollvorgaben, einheitliche Qualitätsmaßstäbe, effektive Prüfprozesse und eine effiziente Dokumentation. Digitale Erfassungssysteme erleichtern die Analyse sowie die nachhaltige Problemlösung. Eine vollständige Fehlerdokumentation verbessert die Ursachenanalyse und die Fähigkeit Prozesse zu optimieren. Zudem wird dadurch eine lückenlose Rückverfolgbarkeit und fundierte Kostenbewertung ermöglicht. Entscheidend ist die aktive Einbindung der Mitarbeitenden. Durch eine standardisierte und lösungsorientierte Kommunikation der Qualitätsprobleme, wird das kollektive Verantwortungs- und Qualitätsbewusstsein in der Belegschaft gestärkt und eine nachhaltige Qualitätskultur etabliert.